MULTI-LAYER CIRCUIT BOARD TECHNOLOGY FOR EFFICIENT CONCENTRATION POLARIZATION BASED W
LOW-POWER EFFICIENT DESKTOP DESALINATION
(Apologies for a non-perfect English below)
(ALSO, MUCH OF THIS DOCUMENT IS IN WRITTEN IN CAPITAL LETTERS GREATLY IMPROVING MY DYSLECTIC HANDICAP AND INCREASING PRODUCTIVITY, THANK YOU FOR YOUR PATIENTS WITH THIS.)
THE IDEA
THE IDEA BOILS DOWN TO THE A COMBINATION OF TWO TECHNIQUES:
A SCALE UP OF THE METHOD “STABILIZATION OF ION CONCENTRATION POLARIZATION USING A HETEROGENEOUS NANOPOROUS JUNCTION”,SEE FOOTNOTE. THIS TEXT DESCRIBES A MEMS TECHNOLOGY SYSTEM BASED ON SILICON WAFER MEMS TECHNIQUES PRODUCING A FLOW OF 20μL/min DESALINATED
USING MULTI-LAYERED PRINTED CIRCUIT BOARD TECHNOLOGY INSTEAD OF SILICON WAFER MEMS TECHNOLOGY
THE DESCRIBED TECHNOLOGY IN THE PAPER ABOVE DISPLAYS A PERFORMANCE THAT FOR THE MOST PART FULL-FILLS THE SEEKERS SPECIFICATION IN THE SEEKER’S CHALLENGE, EXCEPT THAT THE IMPLEMENTED SYSTEM DELIVERS A FLOW ABOUT 4 MAGNITUDES TOO LOW AND MAY BE AN IMPRACTICAL TECHNOLOGY DUE TO VERY HIGH COST OF MEMS PRODUCTION ESPECIALLY FOR LARGER SYSTEMS.
FROM THE ARTICLE:
“...desalination experiment done with natural seawater. The seawater sample was loaded into the reservoir using external pressure pump at the flow rate, 20μL/min. Once ICP is initiated, the depletion zone was formed within 1 sec to divert charged ions into the “salted” stream as shown in Figure 2(a). The ICP layer acts as a virtual barrier for any charged particles (both negative and positive), including most solid particles and biomolecules because their non-zero zeta potential. Therefore, both small salt ions and large microorganisms can be simultaneously removed from the output desalted stream. We confirmed that the desalination operation can be maintained over 1 hour without any membrane clogging ...
In order to quantify the concentration in desalted stream, in situ conductivity measurement of desalted stream was done using embedded microelectrode.The conductivity of the output desalted stream dropped to ~0.5mS/cm (~3mM salinity) from ~45mS/cm (~500mM), the conductivity of original s
eawater. In another experiment with 100mM phosphate buffer solution (~15mS/cm, a model for brackish water), output desalted stream conductivity was also decreased to ~0.3mS/cm (~2mM). From the experiments, the energy effieicy turn out to be ~3.75Wh/L. Therefore, total energy consumption of ICP desalination system would be less than RO facility.
A FLOW OF 20μL/min REQUIRING A 30000 TIMES SCALE-UP TO MEET THE CHALLENGE. HOWEVER, THE AUTHORS ALSO DESCRIBE HOW THE METHOD SCALE BY AREA AND ARGUE THAT A FULL 8 INCH WAFER COULD PRODUCE 18l/h. SCALING TO A FULL WAFER IN SILICONE WOULD BE CUMBERSOME AND EXTREMELY EXPENSIVE.
FROM THE SAME PAPER WE SEE DIMENSIONS OF CHANNELS ETC:
(PICTURE USED FROM WEB WITHOUT PERMISSION)
INSTEAD WE PROPOSE THE USE OF STATE-OF-THE-ART PRINTED CIRCUIT BOARD (PCB) TECHNOLOGY.
PCBS HAS GREAT POTENTIAL AND FLEXIBILITY FOR USE IN MICRO-FABRICATION BUT AT A FRACTION OF THE COST FOR SILICONE MEMS. A CIRCUIT BOARD CAN BE BUILT IN A VARIETY OF MATERIAL, INCLUDING MANY BIO-COMPATIBLE AND STANDARD CBs CAN ALSO BE ALL METAL ETC.
P
IN ADDITION PCBs CAN BE USED TO PRODUCE MUCH LARGER DEVICES AND EVERYTHING COULD GO INTE MASS-PRODUCTION WITH A PUSH OF A BUTTON. IT WOULD ALSO BE CONVENIENT TO DIRECTLY INCORPORATE THE CONTROL ELECTRONICS ON THE SAME CURCUIT BOARD. BELOW WE SEE THE DESIGN RULES FORM A CIRCUIT BOARD SERVICE (MULTI-CB):
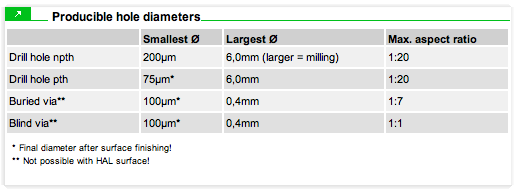
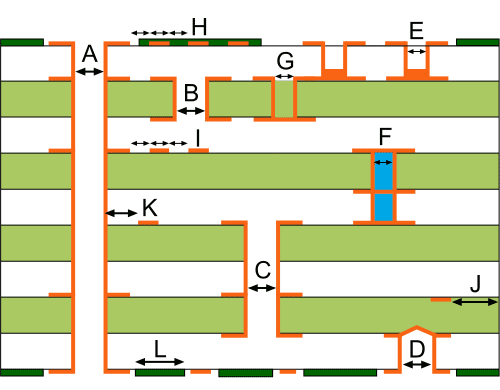
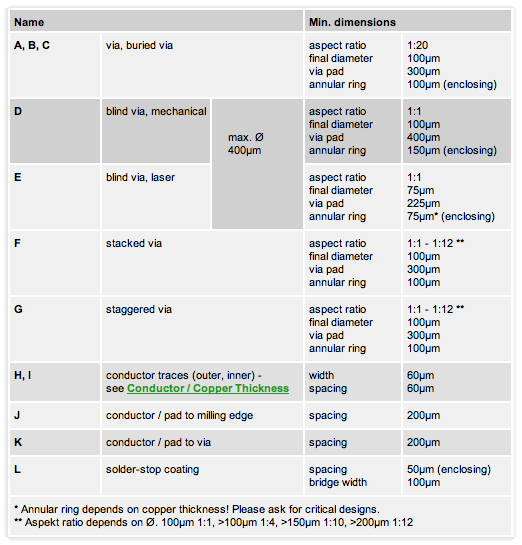
LAYERS OF FOR INSTANCE CONDUCTORS ARE 18 um FROM THIS PARTICULAR COMPANY. THERE ARE RESEARCH ORIENTED CIRCUIT BOARD MANUFACTURERS WITH EVEN HIGHER CAPABILITIES. A BOARD CAN BE 100 LAYERS THICK CORRESPONDING TO A FEW CENTIMETERS MAXIMUM. THE SPECIFICATIONS SEEN ABOVE COULD THEN GO FROM PROTOTYPE INTO DIRECT MASS-PRODUCTION WITH A PUSH OF A BUTTON. WE CAN SEE THAT THE CIRCUIT BOARD TECHNIQUE COULD MEET THE REQUIREMENT OF THE DESCRIBED TECHNOLOGY IN THE PAPER IN TERMS OF SIZES OF CHANNELS AND THICKNESS OF DEVICE. IT IS ALSO POSSIBLE TO MILL ANY PATTERN WITH A 200μM MILL FOR EACH OF THE UP 100 LAYER (IN PCB TERMS BURIED CANELS AND VIAS). IF WE USE THE SCALING LAW FROM ABOVE PAPER AND ASSUME THE WE CAN USE THE PCB TECHNOLOGY THEN WE WOULD NEED A 0.8m X 0.8m CIRCUIT BOARD WHICH IS NO UNUSUAL SIZE, AND IT COULD EVEN GO INTO MASS-PRODUCTION DIRECTLY. THE COST FOR THE PROTOTYPE WOULD BE 1/1000 FOR THE PROTOTYPE AS COMPARED TO A WAFER MEMS AND EVEN BETTER RATIO IN MASS-PRODUCTION.

THE PHYSICAL CONSTRUCTION WOULD CONSIST OF A CONTAINER FOR SALINE WATER ON TOP OF THE PCB WITH A FUNNEL BELOW COLLECTING DESALINATE WATER AND A TUBE FOR CONCENTRATED SALINE WATER OUTPUT, AS DEPICTED BELOW:
THE MOST NATURAL CONSTRUCTION FOR THE MAIN PCB PART WOULD BE A SINGLE PCB WITH WATER DRIVEN BY GRAVITY FROM THE TOP SIDE TO THE BUTTON SIDE, AND WHERE ALL ELECTRICAL CONNECTIONS TO THE MILLIONS OF WATER CHANNELS NEEDED ARE MADE BY NORMAL PCB TECHNOLOGY. THE NAPIAR NEEDED COULD BE LASER-CUT AND INCLUDED IN THE LAYER BONDING PROCESS. IF A COMPLETE STANDARD PROCESS IS PREFERRED THEN TWO HALVES WOULD BE PRODUCED AS TWO CIRCUIT BOARDS AND THE LASER CUT NAPIAR MEMBRANE WOULD BE BONDED MANUALLY BETWEEN THESE.
THE SECOND ALTERNATIVE WOULD BE TO PRODUCE MANY STRIPES OF CIRCUIT BOARDS WHICH CAN BE DOWN TO 200 UM IN THICKNESS AND THEN STACK THEM TOGETHER WHERE EACH BOARD STANDS HORIZONTALLY. THERE MAY BE SOME ADVANTAGES REGARDING FLEXIBILITY OF TOTAL THICKNESS AS WELL AS INTERNAL CHANNEL GEOMETRY BUT IT WOULD BE A SLIGHTLY MORE COMPLEX PROCESS.
CONCLUSIONS
BY COMBING A KNOWN MEMS TECHNOLOGY FOR THE CHALLENGE WITH A PCB TECHNOLOGY WE HAVE SUGGEST HOW THE CHALLENGE COULD BE MET, EVEN IN A QUICKLY MASS-PRODUCIBLE WAY. THERE IS A CAVEAT FOR POWER CONSUMPTION WHICH THE ARTICLE MEASURES SLIGHTLY ABOVE TARGET LEVEL(STILL MOST POWER EFFICIENT METHOD IN THE WORLD) AND IT MAY BE NEEDED TO LOOK AT MORE RECENT TECHNIQUES WHERE FOR INSTANCE MANY JUNCTIONS COOPERATE OR A COMBINATION OF BOTH POSITIVE-REPELLING AND NEGATIVE REPELLING MEMBRANES ARE USED AND WHICH LEADS TO INCREASED POWER EFFICIENCY.
THE SYSTEM COULD ALSO BE BUILT LIKE A WATER TOWER CREATING HIGHER WATER PRESSURE, LARGER OPTIMAL FLOW AND A LOWER POWER CONSUMPTION (DUE TO DECREASED RESISTANCE AT THE DEPLETED REGION OF THE JUNCTION),:
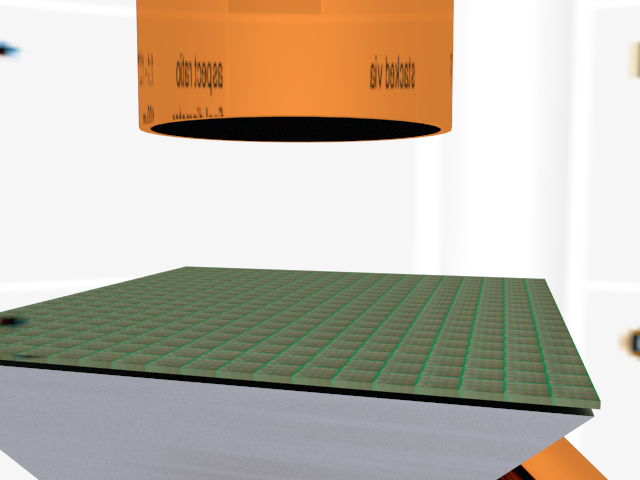